晶圓級封裝/再分布層電路中聚酰亞胺常壓與真空固化工藝對比分析
本文聚焦晶圓級封裝(WLP)/ 再分布層(RDL)電路中聚酰亞胺固化工藝的改進,對比了常壓與真空條件下的固化特性。聚酰亞胺固化的**目標是完成酰亞胺化、優化薄膜附著力、去除殘留溶劑(如 NMP)及光敏成分,需在250°C 至 450°C高溫下進行。真空固化工藝(如 YES-PB12、VertaCure 設備)通過高效脫除溶劑、控制氧含量(<10ppm),相比常壓工藝縮短了時間、避免了褶皺和 “爆米花效應”,且殘留溶劑和氣體量*為常壓工藝的 1/5,***提升了薄膜可靠性與生產效率,為 WLP/RDL 制造提供了更優方案。
思維導圖
一、聚酰亞胺固化的**目標
聚酰亞胺前體轉化為穩定薄膜的固化工藝需實現以下目標,以保障 WLP/RDL 電路的性能:
· 完成酰亞胺化過程(需250°C 至 450°C高溫烘烤);
· 優化薄膜與基底的附著力;
· 徹底去除殘留溶劑(如 N - 甲基吡咯烷酮 NMP)和外來氣體;
· 完全去除光敏成分(避免內應力過大及腔室沉積)。
二、聚酰亞胺固化的關鍵工藝條件
· 可控升溫速率:需匹配聚酰亞胺與基底的熱膨脹系數差異,否則會導致晶圓局部應力變化(表現為薄膜起皺、金屬線變形或分層),影響成品率和可靠性;
· 氧氣含量控制:氧含量需 **<20ppm**,否則會抑制聚酰亞胺交聯,導致薄膜脆化、透明度下降(影響多層工藝對準標記識別),需通過氮氣吹掃或真空環境實現。
三、 常壓固化與真空固化工藝對比

四、 第三方測試結果(EAG)
對 5 微米厚 HD-4000 聚酰亞胺樣品的測試顯示:
· 常壓固化工藝的殘留溶劑和氣體量是真空工藝(YES-PB12 設備)的5 倍
· 真空固化薄膜無氣泡殘留,表面更均勻。
五、真空固化工藝的**優勢
· 縮短工藝時間:無需低溫停留步驟,升溫效率更高;
· 提升薄膜質量:無褶皺、無爆米花效應(無溶劑 / 氣體殘留),薄膜透明(利于多層工藝);
· 降低成本:減少氮氣用量,縮短后續高真空工藝的排氣等待時間;
提高潔凈度:預熱氮氣層流設計優于常壓爐的循環氣流,減少污染物。
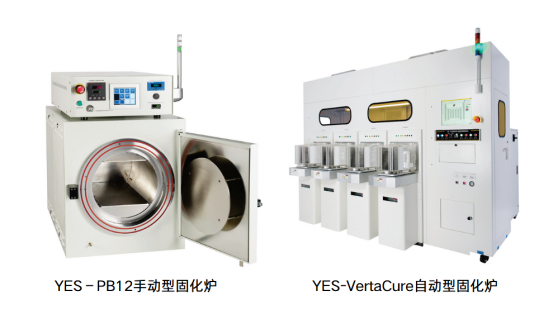
六、 結論
真空環境通過高效脫除溶劑,優化了酰亞胺化速率控制,擴大了工藝窗口,***提升了 WLP/RDL 電路中聚酰亞胺薄膜的可靠性與生產效率,是更優的固化方案。
關鍵問題
聚酰亞胺固化的**目標是什么?為何這些目標對 WLP/RDL 電路至關重要?
**目標包括:完成酰亞胺化、優化薄膜附著力、去除殘留溶劑及光敏成分。這些目標直接影響薄膜的機械(抗應力、附著力)、熱學(耐高溫)和電學性能;若未達成,會導致薄膜起皺、分層、爆米花效應等缺陷,降低 WLP/RDL 的成品率和長期可靠性。
常壓固化與真空固化工藝在溶劑去除和氧氣控制方面的關鍵差異是什么?
l 溶劑去除:常壓工藝依賴高溫和氮氣吹掃,溶劑揮發受擴散限制,需低溫停留且易形成表面表皮(導致殘留);真空工藝利用低壓降低溶劑沸點(如 NMP 在 50 托時沸點 135°C),無表皮形成,溶劑高效去除,無需停留。
l 氧氣控制:常壓工藝需高流量氮氣吹掃,氧含量難穩定;真空工藝通過 3 次真空 / 氮氣吹掃快速除氧,200 托壓力下持續控氧至 < 10ppm,更穩定高效。
真空固化工藝能為 WLP/RDL 生產帶來哪些實際效益?
實際效益包括:①縮短工藝時間(無低溫停留),提升 throughput;②減少氮氣用量,降低成本;③薄膜無缺陷(無褶皺、爆米花效應),提升成品率;④薄膜透明,利于多層工藝對準;⑤減少后續排氣等待時間,提高生產效率。這些優勢共同提升了 WLP/RDL 電路的可靠性與成本效益。
關注我們了解更多內容
YES (Yield Engineering Systems,Inc)
認證的中國授權經銷商:
上海跡亞國際商貿有限公司
Gaia China Co.,Ltd.